Many riders often find themselves frustrated when their ebikes are in need of ebike repairs, leading to longer waiting times than anticipated. Several factors contribute to these delays, such as the availability of parts, the complexity of electrical troubleshooting, and the intricacies involved in battery repairs.
Depending on the specific model of your ebike, sourcing necessary parts can be a challenge, especially when local suppliers operate on an order-on-demand basis, making rare components difficult to obtain. Additionally, many electrical issues present error codes and problems that are not straightforward to diagnose, often requiring specialized expertise. Furthermore, battery repairs demand the attention of highly skilled technicians to ensure compliance with LTA regulations, adding another layer of complexity to the ebike repair process.
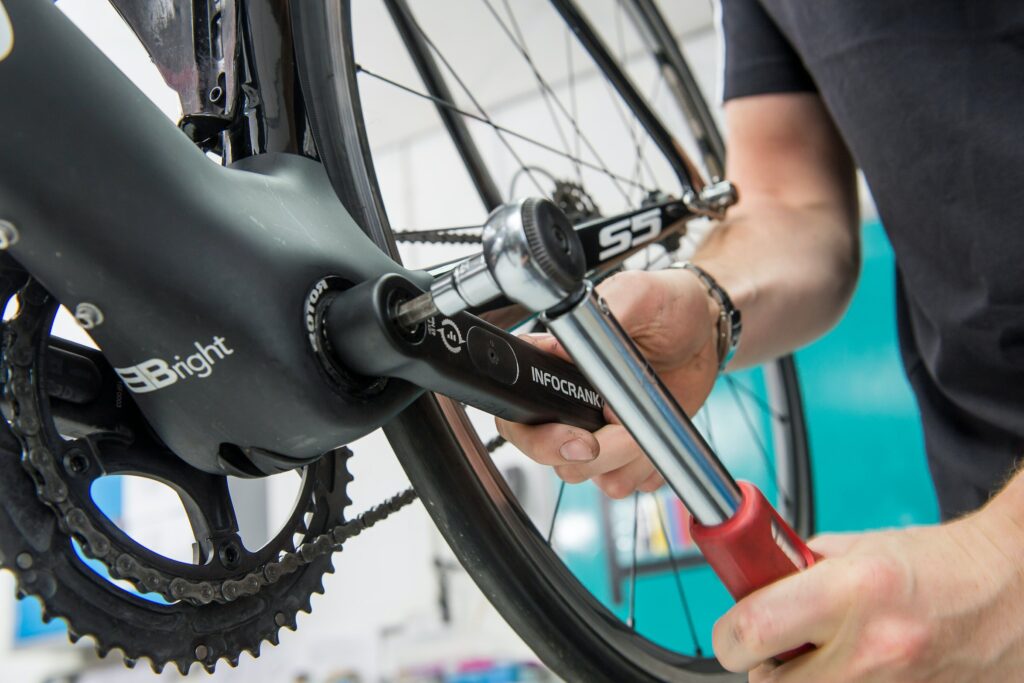
The Challenge of Sourcing Rare Parts
Ebike repair often presents unique challenges, especially when it comes to sourcing rare or specialized components. Unlike traditional bicycles, ebikes rely on advanced systems such as motors, batteries, and controllers, which are not always readily available in local markets. Manufacturers sometimes produce proprietary parts that are specific to certain ebike models, limiting their compatibility and making replacements difficult to find. This scarcity can cause delays in the repair process, leaving owners without their mode of transportation for extended periods.
The global supply chain for ebike parts further complicates the situation. Many components are imported from overseas suppliers, and factors such as shipping delays, customs clearance, or even manufacturing shortages can impact the availability of these parts. Additionally, the rapid evolution of ebike technology means that older models may quickly become obsolete, with discontinued parts no longer in production. For ebike repair shops, this creates the added challenge of sourcing alternatives or retrofitting compatible components, both of which can require significant time and expertise.
While the complexity of ebike repair can be frustrating for riders, understanding the intricacies of sourcing rare parts sheds light on why some ebike repairs take longer than expected. Partnering with a reliable ebike repair shop that has strong supplier connections and industry knowledge can help mitigate delays. For ebike owners, proactive maintenance and regular servicing can reduce the need for rare components, ensuring a smoother and more reliable riding experience.
Impact of Local Supplier Limitations
Additionally, the limitations of local suppliers can affect the overall repair process. Ebike repair isn’t just about swapping out parts; it can also involve complex electrical troubleshooting. Some error codes and recurring problems may not be straightforward to diagnose, requiring a more detailed investigation. This adds an extra layer of time to the ebike repair process, as technicians must thoroughly assess the issues before accessing the required parts. Ultimately, while waiting for parts may be the most visible delay, the intricate nature of diagnosing and repairing ebike issues plays a significant role in extending service times as well.
Electrical Troubleshooting: The Complexity Behind Error Codes
Modern ebikes are equipped with advanced electrical systems that offer convenience and efficiency but can pose challenges when issues arise. Error codes displayed on an ebike’s screen serve as a diagnostic tool, helping riders and technicians identify potential problems. However, interpreting these codes and resolving the underlying issues can be a complex process. The codes often correspond to a wide range of electrical components—such as the motor, battery, controller, or sensors—and identifying the specific fault requires a systematic troubleshooting approach.
The complexity lies in the interconnected nature of the electrical system. A single error code can result from multiple causes, such as a loose connection, a software glitch, or a faulty component. For example, a code indicating a motor issue could stem from damaged wiring, a sensor misalignment, or an internal motor defect. Repair technicians must carefully analyze each possibility, often using specialized tools to pinpoint the problem. This process can be time-intensive, especially if replacement parts are needed or if the issue involves proprietary software that requires manufacturer support.
For ebike owners, understanding the intricacies of electrical troubleshooting underscores the importance of proper maintenance and choosing a trusted repair service. While error codes provide a starting point for diagnosis, resolving electrical issues demands technical expertise and patience. Addressing these challenges promptly can ensure a safer, more reliable riding experience and extend the lifespan of the ebike.
Battery Repair: The Need for Skilled Technicians
Battery repair is one of the most critical aspects of ebike servicing, yet it is also a process that requires significant time and expertise. In Singapore, high-skilled senior technicians are necessary to perform these ebike repairs effectively. This specialization is essential as malfunctions in the battery can lead to severe performance issues or even safety risks.
Moreover, technicians must ensure that the repairs adhere to LTA approved ebike specifications, which adds another layer of complexity and time consumption to the process. With strict regulations in place, ensuring all safety standards are met becomes paramount, indicating that a quick fix is often not feasible. The challenge is compounded by the availability of parts, as many local suppliers may lack the necessary components, making it an order-on-demand situation.
This means that the wait for specific battery parts can extend the duration of the ebike repair process. Electrical troubleshooting further complicates matters, as error codes and recurring problems can be intricate and not easily identifiable. Therefore, the confluence of skilled labor requirements, regulations, and parts availability culminates in the delays experienced when dealing with ebike battery repairs in Singapore.
Mechanical Issues: Time Factors in Common Repairs
When it comes to mechanical issues with your ebike, the types of ebike repairs required can significantly impact the time it takes to get your bike back on the road. Common ebike repairs like tyre changes and brake adjustments can typically be completed in a single seating, making the process relatively quick. However, if your ebike is facing more complex mechanical problems, the time required for diagnostics and repairs can increase.
Depending on your ebike model, the availability of parts plays a vital role; local suppliers might not always have the necessary components in stock, leading to order-on-demand situations that extend repair times. Additionally, electrical issues can complicate repair timelines. Unlike mechanical problems, electrical troubleshooting often involves navigating error codes and recurring issues that can be harder to pinpoint.
This process may require skilled technician expertise, thereby delaying repairs further. Ebike battery repairs present their own challenges, needing highly trained technicians to ensure adherence to LTA-approved ebike specifications. Ultimately, these factors combined mean that while some ebike repairs can be accomplished swiftly, others necessitate a more extended wait, highlighting the complexities involved in ebike repairs in Singapore.
Understanding the Order-on-Demand System
In Singapore, the ebike repair industry faces unique challenges largely due to the order-on-demand system that some local suppliers utilize. Depending on your specific ebike model and the rarity of its parts, obtaining the necessary components can take longer than anticipated. Many local bike shops may not keep a comprehensive inventory of every part, especially for less common models.
When parts are not readily available, the ebike repair process can be significantly delayed as the technician waits for the required components to arrive, leaving customers frustrated and uncertain about their ebike‘s return. This situation highlights the importance of choosing an ebike model with readily available replacement parts if you want to minimize repair times in the future. Additionally, electrical troubleshooting in ebikes can complicate the repair timeline further.
Unraveling error codes and diagnosing duplication of problems are often not straightforward tasks requiring skilled technicians. In some instances, the need for specialized tools or diagnostic equipment may prolong the repair process. Furthermore, issues related to battery repairs demand high-level expertise and adherence to LTA approved ebike specifications, which can lead to extended waiting times as these tasks are performed by senior technicians. All these factors contribute to a more complicated repair process in Singapore’s ebike service landscape.
Compliance with LTA Specs: A Necessary Delay
In Singapore, compliance with the Land Transport Authority (LTA) specifications is paramount, particularly when it comes to the ebike repair. This adherence ensures that all ebike repairs meet stringent safety and performance standards. When a repair is required, technicians must assess whether the work aligns with these regulations, which can often lead to delays.
For example, battery repairs are not just mechanical fixes; they require high-skilled senior technicians who have the expertise to ensure that the unit remains compliant with LTA-approved specifications. This meticulous attention to detail is necessary but contributes to longer turnaround times for ebike repair services in the region. Moreover, certain ebike models may have parts that are challenging to source.
Local suppliers may be limited in their inventory, and some parts are on an order-on-demand basis. Delays can arise when repairs require specialized components that are not readily available. Additionally, electrical troubleshooting can be complex, as error codes and issues may not be straightforward to diagnose, prolonging the repair process. Consequently, the combination of compliance requirements and the variability in parts availability makes it evident why ebike repairs can take longer than one might expect in Singapore.
The Importance of Quality Over Speed in Repairs
In the world of ebike repairs, quality often takes precedence over speed, especially in Singapore. With various models on the market, each with unique components, sourcing the right parts can be a challenge. Depending on your ebike model and the rarity of its parts, some local suppliers may not have what you need readily available and operate on an order-on-demand basis.
This can lead to delays as you wait for the necessary components to arrive, ensuring that the repair technician has everything on hand to perform a thorough and effective repair. Thus, prioritizing quality in sourcing and fitting the right components can significantly extend the repair timeline but leads to better long-term functionality of the ebike. Furthermore, the complexity of electrical troubleshooting adds another layer to repair duration.
Some error codes and repeated problems are not straightforward and require in-depth diagnosis by skilled technicians. Battery repair also necessitates high-skilled senior technicians, especially to maintain adherence to LTA-approved specifications. This careful consideration of quality in the ebike repair process not only ensures that the ebike functions optimally but also significantly contributes to rider safety, validating the extended repair times as completely justified.
Navigating the Challenges of Ebike Repairs
Understanding the complexities behind ebike repairs is crucial for both owners and enthusiasts. With numerous factors influencing repair times, such as the availability of rare parts and the expertise required for electrical troubleshooting and battery repairs, it’s clear why waiting for service can be frustrating. Local suppliers may not always stock the parts needed, leading to potential delays in order fulfillment.
Additionally, errors in electrical systems can be challenging to diagnose, especially if the issues recur, requiring a thorough and thoughtful approach from technicians. Moreover, battery repairs present their own unique challenges, as they demand skilled technicians who are well-versed in LTA approved specifications.
While more straightforward ebike repairs, like tyre changes and brake issues, can often be handled expeditiously, comprehensive repairs necessitate time and expertise. Therefore, it is essential for ebike users to be patient and understand the intricacies involved in the repair process, ultimately ensuring that their ebikes are safe and fully functional for the road ahead.
I’m a DIY enthusiast and found this post really informative. The discussion of LTA specifications and the intricacies of battery repairs made me realize how much I still have to learn.
Hi Emilie, we’re glad you found the post informative! As a DIY enthusiast, it’s great that you’re taking the initiative to learn more about ebike repairs. If you have any further questions or need guidance, please feel free to reach out to us at [email protected] or +65 6589 8877. We’re always here to help. Good luck with your learning journey, and we hope to see you around!
The author is spot on! I’ve seen many ebikes on the road with poorly done repairs, which can lead to accidents. It’s great that this blog is raising awareness of the importance of proper repairs.
Thank you for sharing your concern, Rajeswari. We completely agree that proper ebike repairs are crucial for safety and functionality. At Eko Life, we prioritize quality over speed and ensure our technicians are trained to meet LTA specifications. If you have any more questions or concerns, feel free to reach out to us at [email protected] or +65 6589 8877.
I totally understand the pain of ebike repairs in Singapore. I once had to wait for weeks to get a replacement battery. It’s a pity that quality repair services are often not as convenient as quick fixes.
Thank you for sharing your ebike repair experience, Kai Wen Low. We understand the frustration that comes with waiting for replacement parts, especially batteries. At Eko Life, we prioritize quality over speed, ensuring that our customers receive thoroughly inspected and certified repairs that meet LTA specifications. While it may take some time, we want to assure you that our skilled technicians are dedicated to providing the best possible service for your ebike. If you have any further questions or concerns, please don’t hesitate to reach out to us via [email protected] or +65 6589 8877.