Ebike repairs in Singapore can often be a frustrating experience for riders awaiting quick fixes to get back on the road. With the growing popularity of ebikes, the demand for ebike repairs has surged, yet many find themselves facing unexpected delays. Factors such as the availability of parts, particularly for unique or less common ebike models, heavily influence repair times.
Local suppliers may not always have the necessary components in stock, leading to longer waiting periods as they may operate on an order-on-demand basis. Moreover, electrical troubleshooting can complicate matters further, as certain error codes may not have straightforward solutions. As we delve deeper into the various reasons behind these delays, we will also explore specific ebike repair needs such as battery issues and common mechanical problems that contribute to extended servicing times.
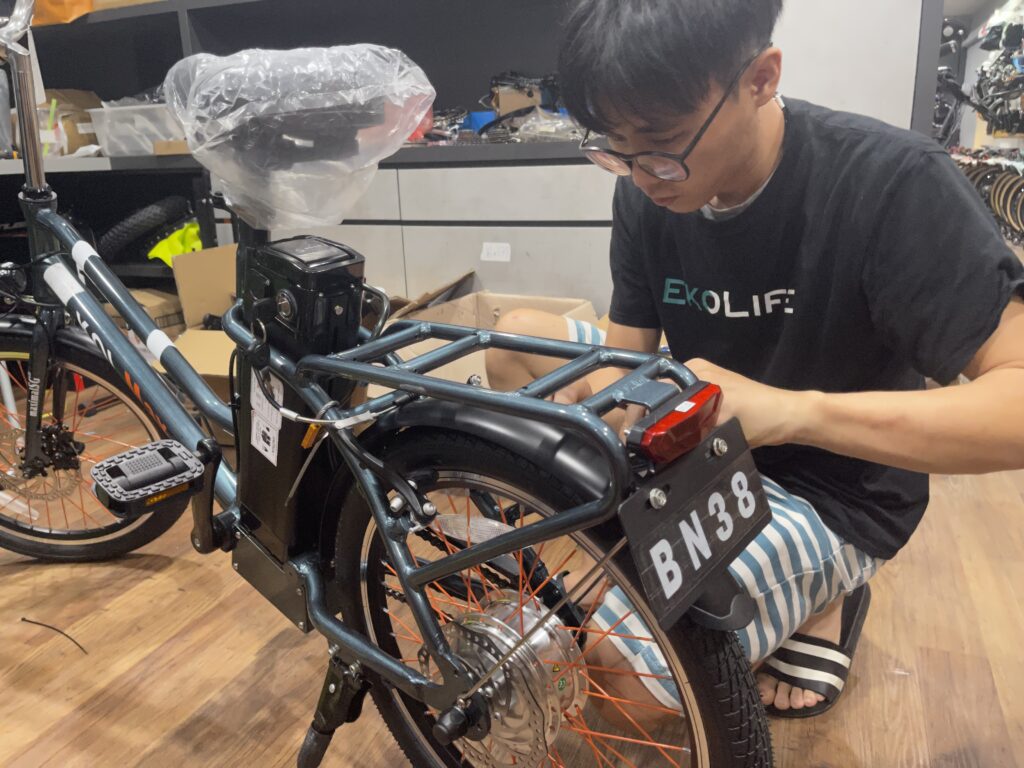
Availability of Spare Parts and Local Supply Challenges
One of the primary reasons ebike repairs can take a considerable amount of time in Singapore is the availability of spare parts paired with the local supply challenges. Depending on your ebike model, the rarity of certain components plays a significant role in repair timelines. Some local suppliers may lack essential parts and rely on an order-on-demand basis, which can further prolong the repair process.
This situation is especially prevalent with specialized or less common ebike models that require specific parts that are not readily available in the local market. Consequently, waiting for these parts to arrive can lead to frustrating delays for ebike owners seeking quick repairs. Additionally, the complexity of electrical troubleshooting can also contribute to extended ebike repair times. Some error codes and recurring issues aren’t as straightforward to diagnose, necessitating a meticulous approach from technicians to identify and rectify the problems.
Furthermore, battery repairs present their own challenges as they require high-skilled senior technicians to ensure the procedures align with the Land Transport Authority (LTA) approved ebike specifications. This demand for specialized knowledge, alongside supply chain issues, highlights the multifaceted challenges that can delay ebike repairs in Singapore, underscoring the importance of patience and understanding in this process.
Complexity of Electrical Troubleshooting and Error Codes
One of the primary reasons ebike repairs can take time in Singapore is the complexity of electrical troubleshooting. Many modern ebikes come equipped with intricate electrical systems that can present challenges when identifying underlying issues. Error codes, while intended to provide clarity, can often complicate the diagnostic process.
Repair technicians may encounter duplicative problems or misleading codes that require additional time and expertise to unravel. This detail-oriented approach is crucial, as a quick fix might mask deeper issues that could cause further complications if not properly addressed. Furthermore, the rarity of some ebike parts often adds to the timeline of repairs.
Depending on the specific model and availability, local suppliers may not carry the necessary components in stock, leading to an order-on-demand situation. While routine maintenance such as tyre changes and brake adjustments can often be handled quickly, more complex electrical issues will require skilled technicians to ensure that repairs adhere to LTA-approved ebike specifications. This meticulous attention to detail and potential wait times for parts makes repairing ebikes a more time-consuming process than one might initially expect.
The Importance of Skilled Technicians for Battery Repairs
When it comes to ebike repairs, particularly for battery issues, the importance of skilled technicians cannot be overstated. Battery repairs require a high level of expertise and precision, as improper handling can lead to significant complications. In Singapore, these tasks are typically reserved for senior technicians who have undergone extensive training and possess years of experience.
Given the specialized nature of ebike batteries, it becomes crucial for repair shops to ensure that their technicians are well-versed in maintaining the standards set by the Land Transport Authority (LTA). This added layer of scrutiny and skill inevitably contributes to longer repair times, as not just anyone can perform these delicate procedures safely and effectively. Moreover, the rarity of certain ebike parts can exacerbate these delays.
Depending on the model, some components may not be readily available, leading these repairs to operate on a order-on-demand basis from local suppliers. Furthermore, electrical troubleshooting can be complex; error codes can signify various issues, many of which are not straightforward to diagnose or resolve. Collectively, these factors reinforce the necessity for skilled technicians while contributing to the overall time consumed in the ebike repair process in Singapore.
Impact of Ebike Model Rarity on Repair Times
One of the significant factors influencing the time taken for ebike repairs in Singapore is the model rarity of the ebike itself. Depending on the specific model and brand, the availability of spare parts can vary greatly. Local suppliers often face challenges in maintaining stock for less common models, sometimes requiring an order-on-demand approach to procure necessary components. This can lead to extended waiting times as repairs are contingent upon the arrival of these rare parts, leaving customers frustrated and wondering about the delay.
Manufacturers of popular models may have more readily available parts, but those with niche or less popular choices could find themselves facing much longer repair timelines. Additionally, the complexity of the repairs can also hinder prompt service. Many ebike repairs are not straightforward, especially when it comes to electrical issues and battery-related problems. Error codes may not be clearly defined, and duplicating certain issues can further complicate troubleshooting.
High-skilled senior technicians are often required, especially for battery repairs that must align with LTA-approved specifications. Thus, the downtime for ebikes can be a combination of waiting for parts and the meticulous nature of the repair work involved.
Common Ebike Repairs and Their Time Requirements
Ebike repairs can vary significantly in time depending on the specific issues and the model of the ebike. Common ebike repairs like tyre changes and brake-related issues typically have a quicker turnaround, often completed within the same day when parts are readily available. However, if a mechanical problem arises that requires specialized tools or more intricate work, the ebike repair duration could extend.
This is particularly relevant in Singapore, where parts for certain ebike models may not be readily stocked by local suppliers, leading to a wait time as parts are ordered on demand. More complicated repairs, such as electrical troubleshooting, can further lengthen the process. Error codes may not always be straightforward, requiring skilled technicians to accurately diagnose and rectify the issues.
Additionally, battery repairs necessitate a high level of expertise, as only senior technicians should handle these sensitive components to ensure compliance with LTA regulations. The combination of parts scarcity and the intricacies of electronic and battery repair work contributes to the overall longer repair times for ebikes in Singapore, making it crucial to understand these challenges when seeking servicing.
Understanding Order-on-Demand Parts and Its Implications
In Singapore, the efficiency of ebike repair services can often be hindered by the reliance on order-on-demand parts. Depending on your ebike model and the availability of specific components, some local suppliers may struggle to keep essential parts in stock. This can lead to frustrating delays as repair shops must wait for the ordered parts to arrive before they can proceed with the necessary fixes.
The situation is particularly pronounced for rarer models, which might require specialized parts that aren’t immediately accessible in the local market. Hence, what might seem like a straightforward repair can stretch out due to supply chain constraints. Moreover, electrical troubleshooting presents another layer of complexity that contributes to prolonged repair times.
Many ebike error codes and recurring issues are not easily identifiable, requiring skilled technicians to conduct thorough diagnostics. The delicate nature of battery repairs also plays a significant role, as highly-skilled technicians are needed to ensure that any repairs stay within LTA-approved specifications. Thus, while basic repairs such as tyre changes or brake adjustments might be tackled quickly, intricate issues often demand more time, ultimately adding to the overall repair duration in Singapore.
Regulatory Compliance and LTA Approved Specifications
In Singapore, ebike repairs are heavily influenced by stringent regulatory compliance and LTA (Land Transport Authority) approved specifications. Any ebike repair or modification done to an ebike must adhere to these regulations to ensure safety and performance. This regulation not only requires technicians to possess specialized knowledge but also limits the types of components that can be used in ebike repairs.
Consequently, sourcing LTA-approved parts can be challenging, especially for rare ebike models, which may force suppliers to operate on an order-on-demand basis. As a result, waiting for the right parts can contribute significantly to repair times. Additionally, the complexity of certain ebike repairs, such as electrical troubleshooting and battery repairs, further complicates the repair process.
Error codes may be ambiguous, and diagnosing recurring issues can be time-consuming, necessitating a high level of expertise. Battery repairs are particularly intricate and demand skilled senior technicians to ensure compliance with LTA specifications. Thus, the cumulative effect of regulatory requirements, the rarity of parts, and the technical challenges involved in repairs leads to extended wait times for ebike owners in Singapore.
Navigating the Complexities of Ebike Repairs
In conclusion, understanding the intricacies involved in ebike repairs can shed light on the often lengthy waiting periods that bike owners face. From sourcing rare parts to navigating electrical troubleshooting, the reality is that each repair requires a significant amount of skill and time. With varying models and the potential for unique error codes, what may seem like a simple fix can become a more complex challenge within a workshop setting. Additionally, some supplies are only available on an order-on-demand basis, further prolonging the process for many users seeking quick solutions.
Moreover, not all repairs are created equal, especially when it comes to more intricate components like battery systems. Battery repairs necessitate the expertise of senior technicians, as they ensure compliance with LTA-approved specifications. This means that while common repairs such as tyre changes and brake adjustments can be done relatively quickly, more specialized work will inevitably take longer. Ultimately, patience is necessary for ebike repairs, but knowing the factors behind these delays can help riders make more informed decisions about their ebike maintenance and repair needs.
The reliance on order-on-demand parts seems like the main bottleneck. What are some potential solutions to this issue?
Thank you for pointing out the issue, Lokman Hakim! You’re right, the reliance on order-on-demand parts can indeed cause delays. One potential solution could be for e-bike manufacturers to maintain a more comprehensive inventory of spare parts, including unique or less common models. This way, repair shops like Eko Life can access the necessary parts promptly. Additionally, investing in advanced infrastructure, such as 3D printing or spare part production in-house, could help reduce reliance on external suppliers. At Eko Life, we’re exploring these options and exploring partnerships with suppliers who can offer more rapid shipping and custom part production. If you have any further insights or suggestions, please don’t hesitate to share them with us. Contact us directly at [email protected] or +65 6589 8877.
As someone who uses ebikes daily, the complexity of repair procedures is something I’m not aware of. Thanks for shedding light on it!
Hello Kavin, thank you for your thoughtful comment! We understand that the intricacies of ebike repair can be overwhelming, but it’s great that you’re taking the initiative to learn more about it. If you have any further questions or concerns about ebike maintenance and repairs, please don’t hesitate to reach out to us at [email protected] or call us at +65 6589 8877. We’re here to help. Have a pleasant ride!
I completely understand the frustration of delayed ebike repairs. Wish there was a more reliable way to source spare parts for less common models.
We at Eko Life understand the challenges of sourcing spare parts for unique or less common e-bike models. While we can’t guarantee instant availability, we do offer a guarantee for all LTA-approved e-bikes. We would be happy to discuss possible solutions with you and explore ways to minimize repair delays. Please feel free to contact us at [email protected] or +65 6589 8877 to explore further assistance.